Project:
Optimized chassis mounts for Tesla electric vehicles
Order:
Optimization of chassis bearings for well-known electric vehicles. Problem: The OEM quality is not sufficient for the customer, as the bearings wear out quickly and the driving experience deteriorates.
Inventory:
The bearings sent to us are examined and measured. The manufacturer uses rubber, which tears under higher loads. We not only look at the structure of the bearing, but also at the partner component to which it is bolted. This gives us information about the requirements of the bearing and in which directions forces are absorbed and which lines of freedom should/must be restricted. We quickly recognized this: We need to change the type of bearing. So we designed a sleeve with a mount for a ball spherical plain bearing. The outer dimensions of the sleeve must meet tight tolerances so that it can be pressed into the control arm without any problems, for example, and at the same time the ball joint bearing must be pressed in without play. Determining the correct tolerance is therefore extremely important. It is also important that the tolerances are adhered to during production.
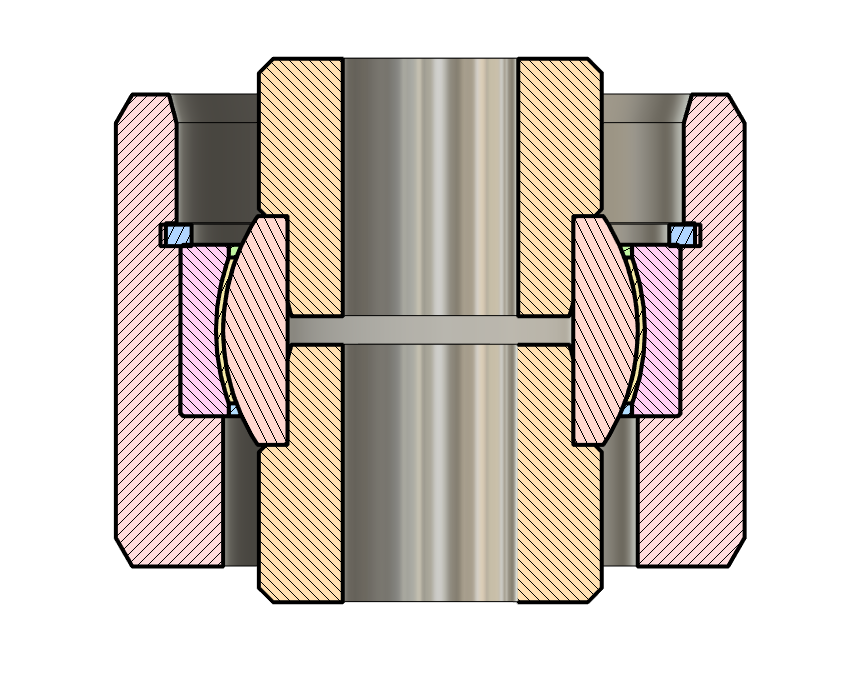
What can it be?
We either supply the data and drawings so that the customer can manufacture the parts themselves, or we offer the hardware.
How much can it be?
The customer only needs a small number of units, as he uses them to serve his workshop customers and installs the parts himself. This is not a problem, because the quantities do not matter to us.
Fancy a little color?
The component is given a layer of hard anodizing and a laser engraving with an identification defined by the customer.